Thrust Ranges
We have developed thrusters from 0.005 Newtons to 22 Newtons using a variety of monopropellants including hydrogen peroxide, hydrazine, tridyne gas and cold gas. Each type of system has unique benefits and aspects. We would be glad to discuss your microthruster propulsion needs to determine the best fit for your system. Hydrogen peroxide offers moderate monopropellant performance in a "green" propellant package. Hydrazine has higher performance and is used in many US government propulsion systems. Tridyne (a mixture of nitrogen, hydrogen, and oxygen gas) microthrusters have also been developed. These have the advantage of cold gas safety and performance comparable to hydrogen peroxide. This provides a safe, non-toxic propulsive alternative for cubesats and other nanosatellites.
Below is an Image displaying a size comparison of one of our thrusters:
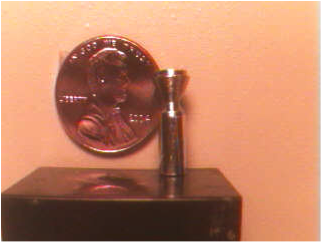
Thruster Testing
The image below shows our thruster testing station. We use this to test many variables including thrust and pulse life. A table displaying data collected by our testing station is positioned below the testing station picture.
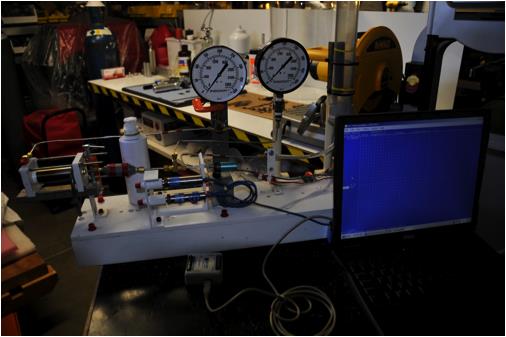
M005HP | M010HP | M050HP | M100HP | M005 | M010 | M050 | M100 | |
---|---|---|---|---|---|---|---|---|
Thrust (N) | 0.005 | 0.1 | 0.5 | 1.0 | 0.005 | 0.05 | 0.5 | 1.0 |
Isp (sec.) | 100 | 110 | 120 | 120 | 150 | 160 | 170 | 200 |
Inlet Pressure (Pa) | 350000 | 350000 | 350000 | 350000 | 350000 | 350000 | 350000 | 350000 |
Minimum Impulse bit (N-sec) | 1.2x10^-4 | 9*10^-4 | 4x10^-3 | 8.5x10^-3 | 1.7x10^-4 | 6x10^-3 | 3x10^-2 | 3x10^-2 |
Weight (grams) | 10 | 11 | 15 | 20 | 10 | 12 | 15 | 30 |
Exit Diameter (mm) | 3.81 | 5 | 6.35 | 7.6 | 3.81 | 4.45 | 8.9 | 8.9 |
Pulse Life | >500,000 | >500,000 | >500,000 | >500,000 | >100,000 | >100,000 | >100,000 | >100,000 |
Power (W) | 0.5 | 0.5 | 1.0 | 2.0 | 0.5 | 0.5 | 1.0 | 2.0 |
Thruster design
We can develop custom thruster systems integrating a variety of different valves types. Examples include refrigerant-based propellant thrusters and nitrous oxide-alcohol systems.
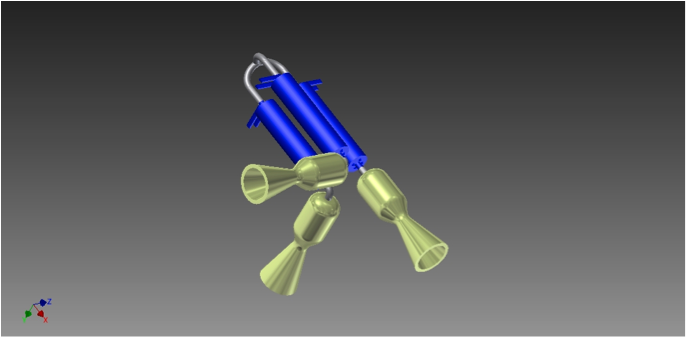
Propellant Design and Testing
We have a variety of thrust stand systems that can measure thrust from milli-Newtons to Newtons. We can also measure temperatures, pressures and flow rates and customize testing to your needs. We are always interested in evaluating new and promising propulsion systems and work with universities and other research organizations to evaluate these technologies. We have designed a gel-propellant system to boost a microspacecraft from Low-Earth Orbit to a higher orbit. A gel propellant system offers a microspacecraft propulsion module with lower mass and volume yet the same performance as a solid motor (Isp currently of a solid is approximately 290 seconds). It is also safer since it is not susceptible to electrostatic discharge or leakage. It is safe and versatile to fit the delta-v requirements of many different microspacecraft missions. It is more efficient than hybrid propulsion modules since it does not suffer from a change from optimum mixture ratio as it is throttled or variations in propellant burn rate.
The gel-propellant makes it possible to use the addition of inert gels to permit programming of the oxidizer and fuel. A single pressurization system can be incorporated with the novelty of pressurizing both components in one tank, decreasing both system mass and volume. This project characterized gel-propellants and provided a recommendation for a propellant combination.
Some missions require the higher performance of a bi-propellant propulsion system. We have used our experience with hydrogen peroxide propulsion systems to create a bi-propellant hydrogen peroxide-kerosene engine system. This unit can operate at 150 pounds of thrust in bi-prop mode using the heat of decomposition of hydrogen peroxide to autoignite kerosene injected into the chamber. The system can also operate in monoprop mode as a simple hydrogen peroxide thruster.
Catalyst Design and Testing
The catalyst is a vital part of a monopropellant thruster. MAS has addressed this and hasdesigned a unique catalyst for the hydrogen peroxide thrusters. In most monopropellant systems a bed of catalytic pellets is supported by screens. That arrangement has a tendency to degrade in performance over time and the pellets will often crack and blow through the retaining screen when they are too big for a microthruster. We use an innovative metal gauze catalyst design which offers increased system performance and lifetime. Other microthrusters have had difficulty maintaining proper decomposition of the propellant in the chamber, but our system has operated for over 500,000 pulses with proper decomposition.
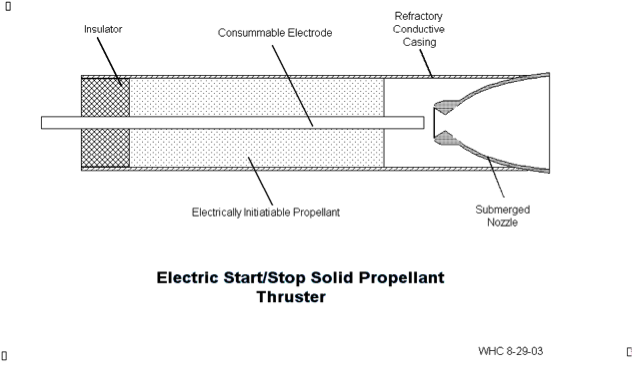
Electric Propulsion
We have consulted on electric propulsion system development and analysis. We have defined system development steps and requirements to progress the electric propulsion technology to a higher technology readiness level. We have a partnership with an electric propulsion company to provide electric propulsion solutions for a variety of potential small satellite applications.